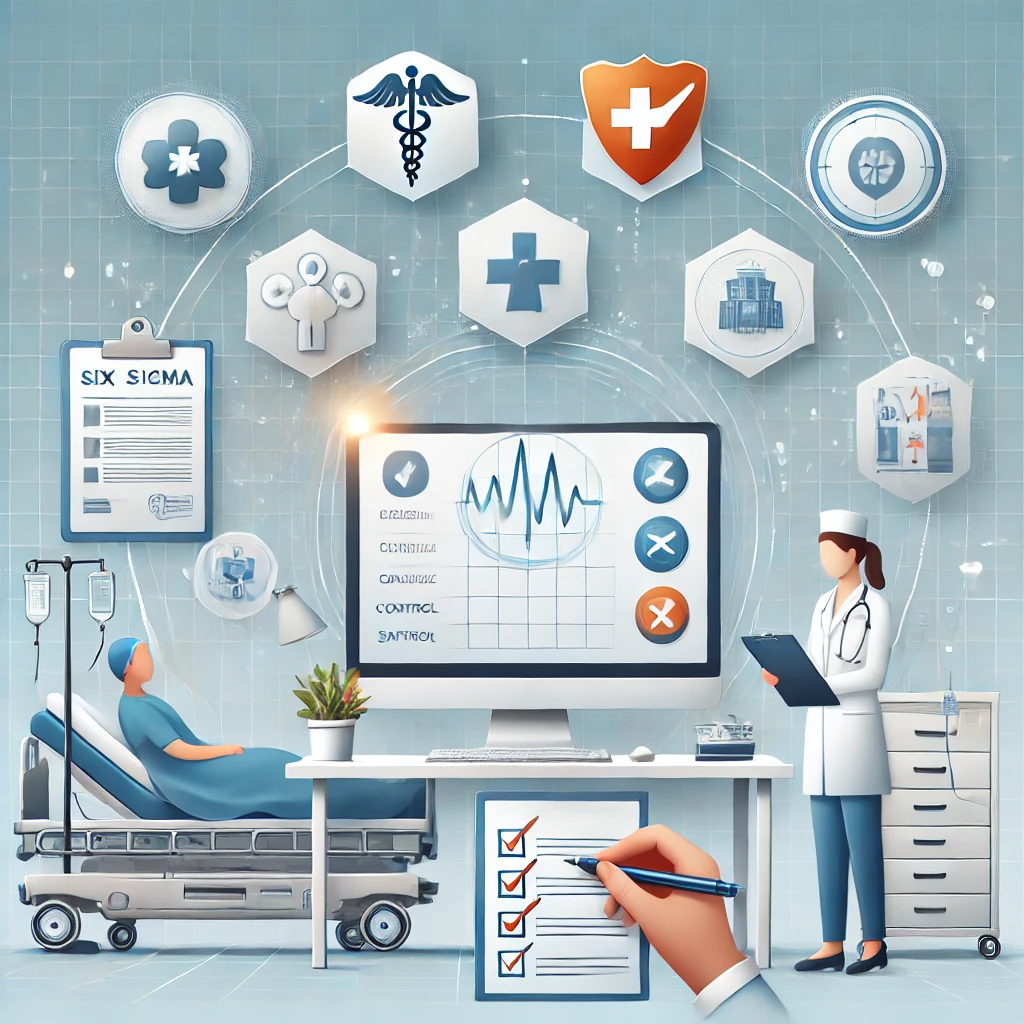
Lean Six Sigma Project at Urgent Care Center: A Detailed Guide
Table of Contents
- Introduction to Lean Six Sigma in Healthcare
- Identifying Challenges in Urgent Care Centers
- How Lean Six Sigma Can Improve Urgent Care
- Key Steps to Implement a Lean Six Sigma Project
- Case Study: Reducing Patient Wait Times
- Best Practices for Lean Six Sigma in Urgent Care
- Tools and Software for Lean Six Sigma in Healthcare
- Conclusion and Next Steps
Introduction to Lean Six Sigma in Healthcare
Lean Six Sigma is a powerful methodology for improving efficiency and reducing waste, making it an ideal solution for challenges faced by urgent care centers. By focusing on validated variables (Xs) that impact outcomes, Lean Six Sigma ensures sustainable improvements in patient care and operational efficiency.
Identifying Challenges in Urgent Care Centers
Urgent care centers face unique challenges, including:
- Long patient wait times: A leading cause of patient dissatisfaction.
- Inefficient resource utilization: Overburdened staff or underused facilities.
- High operational costs: Due to redundant processes and errors.
- Inconsistent care delivery: Leading to varying patient outcomes.
How Lean Six Sigma Can Improve Urgent Care
Lean Six Sigma addresses these issues by:
- Streamlining patient flow: Reducing bottlenecks in triage and treatment processes.
- Optimizing resource allocation: Ensuring staff and equipment are used efficiently.
- Improving patient outcomes: Standardizing care processes to reduce errors.
- Enhancing patient satisfaction: Minimizing delays and improving communication.
Key Steps to Implement a Lean Six Sigma Project
Step 1: Define
- Goal: Clearly define the problem and objectives. For example, “Reduce patient wait times by 30%.”
- Tools: SIPOC diagrams (Suppliers, Inputs, Process, Outputs, Customers) and project charters.
Step 2: Measure
- Data Collection: Gather baseline data on key metrics, such as average patient wait time or staff utilization rates.
- Tools: Process maps and control charts to visualize and monitor the process.
Step 3: Analyze
- Root Cause Analysis: Identify factors contributing to inefficiencies.
- Tools: Fishbone diagrams, Pareto charts, and regression analysis to pinpoint validated Xs.
Step 4: Improve
- Solutions: Implement targeted interventions, such as:
- Streamlining triage protocols.
- Introducing digital check-in systems.
- Redesigning staff schedules to align with peak times.
- Tools: Design of Experiments (DOE) and pilot testing.
Step 5: Control
- Monitoring: Establish controls to sustain improvements.
- Tools: Control charts and dashboards for ongoing tracking of key performance indicators (KPIs).
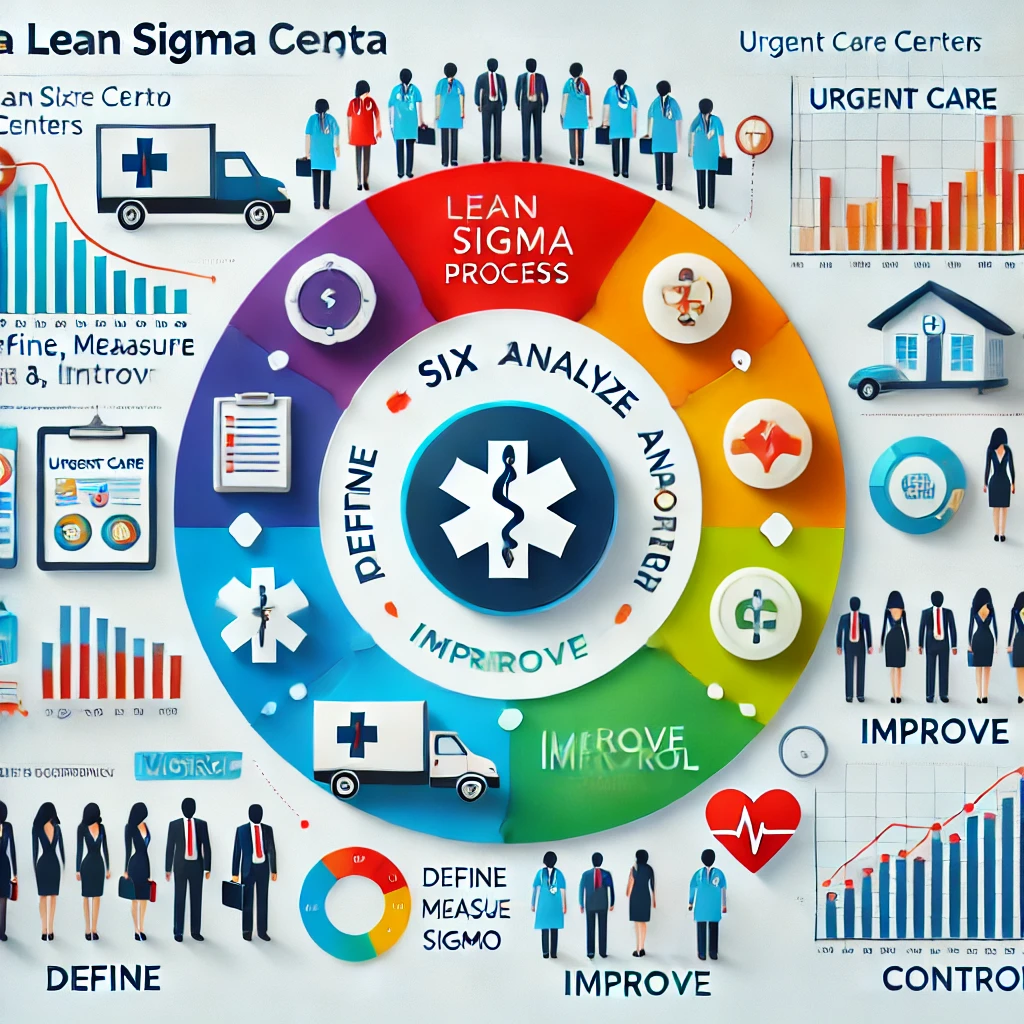
Lean Six Sigma Project at Urgent Care Center
Case Study: Reducing Patient Wait Times
Background
An urgent care center faced complaints about long patient wait times, averaging 90 minutes per visit. Using Lean Six Sigma, the goal was to reduce this to under 60 minutes.
Approach
- Define: The project focused on reducing wait times during peak hours.
- Measure: Data showed triage delays and uneven staff workloads.
- Analyze: Fishbone analysis identified bottlenecks in the check-in process and inconsistent triage practices.
- Improve: Introduced:
- Online pre-registration.
- A fast-track lane for non-critical cases.
- Staff reallocation based on real-time demand.
- Control: Implemented dashboards to monitor daily wait times.
Results
- Wait times dropped to 50 minutes on average.
- Patient satisfaction scores increased by 25%.
Best Practices for Lean Six Sigma in Urgent Care
- Engage Stakeholders: Involve staff at all levels to gain buy-in and insights.
- Focus on Patient-Centric Metrics: Prioritize KPIs like wait times, error rates, and satisfaction scores.
- Adopt Iterative Improvements: Regularly revisit and refine processes.
Tools and Software for Lean Six Sigma in Healthcare
- Minitab: For statistical analysis and control charts.
- Lucidchart: For process mapping and SIPOC diagrams.
- Tableau: For data visualization and performance dashboards.
- iGrafx: For process modeling and simulation.
- Google Sheets: For real-time collaboration on data tracking.
Conclusion and Next Steps
Lean Six Sigma is a proven approach to tackling the operational challenges of urgent care centers. By following the DMAIC methodology and leveraging validated Xs, centers can achieve measurable improvements in efficiency and patient satisfaction. Begin your journey today by identifying a key issue in your center and applying these principles to drive meaningful change.
Lean Six Sigma Metrics for Urgent Care Centers
Key Performance Indicators (KPIs)
- Average Patient Wait Time: Measure time from check-in to being seen by a provider.
- Patient Throughput: Track the number of patients processed per hour or day.
- Staff Utilization Rates: Monitor the efficiency of resource allocation.
- Error Rates: Count errors in patient records, prescriptions, or treatments.
Measuring Success
Implement tools like control charts and dashboards to track improvements over time and identify areas needing further adjustments.
Lean Six Sigma Project at Urgent Care Center
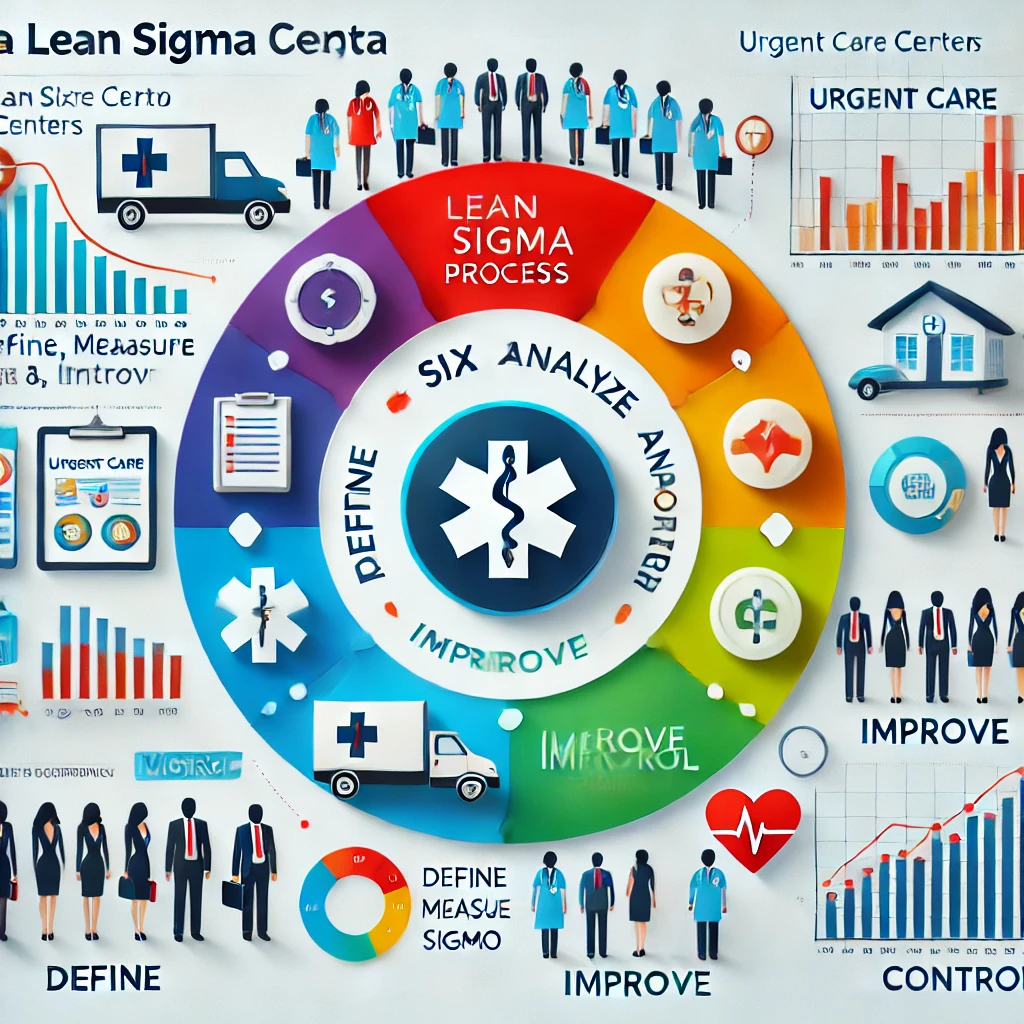
Examples of Successful Lean Six Sigma Projects in Healthcare
Example 1: Optimizing Triage Efficiency
- Problem: High variability in triage times leading to inconsistent patient flow.
- Solution: Streamlined triage protocols and introduced electronic documentation tools.
- Outcome: Reduced triage time by 40%, improving overall patient throughput.
Example 2: Reducing Medication Errors
- Problem: Frequent errors in prescription handling at discharge.
- Solution: Implemented barcode scanning for medication verification.
- Outcome: Achieved a 95% reduction in medication errors within three months.
Advanced Lean Six Sigma Techniques for Healthcare
Value Stream Mapping (VSM)
- Purpose: Identify waste in processes and visualize current and future states.
- Application: Map patient flow from check-in to discharge, highlighting bottlenecks.
Failure Mode and Effects Analysis (FMEA)
- Purpose: Anticipate and mitigate risks in critical processes.
- Application: Use FMEA to evaluate triage or lab testing procedures.
Lean Six Sigma Roles in Urgent Care Projects
Key Roles and Responsibilities
- Project Champion
- Role: Provides oversight, secures resources, and removes barriers.
- Responsibilities: Acts as a liaison between the team and executive leadership.
- Process Owner
- Role: Ensures project improvements are sustained.
- Responsibilities: Oversees daily operations and ensures adherence to changes.
- Green Belt/Black Belt Practitioners
- Role: Lead and execute the Lean Six Sigma project.
- Responsibilities: Use tools like DMAIC and validated Xs to achieve project goals.
- Team Members
- Role: Support specific tasks and contribute domain expertise.
- Responsibilities: Assist in data collection, brainstorming solutions, and implementation.
Lean Six Sigma Project at Urgent Care Center
The Role of Patient Feedback in Lean Six Sigma
Collecting Feedback
- Methods: Use surveys, suggestion boxes, and post-visit interviews.
- Key Questions:
- “How satisfied are you with your wait time?”
- “Were staff responsive to your needs?”
Incorporating Feedback
- Use feedback data to validate variables (Xs) affecting patient satisfaction.
- Identify recurring themes in complaints or suggestions for targeted improvements.
Addressing Resistance to Change in Urgent Care Centers
Common Sources of Resistance
- Staff Concerns: Fear of increased workload or job insecurity.
- Cultural Barriers: Resistance to adopting new processes or technologies.
Strategies to Overcome Resistance
- Engage Stakeholders: Involve staff early in the project for their input and buy-in.
- Clear Communication: Explain the benefits of Lean Six Sigma for staff and patients.
- Training Programs: Equip staff with skills to adapt to changes confidently.
Cost-Benefit Analysis for Lean Six Sigma Projects
Direct Benefits
- Reduced Operational Costs: Streamlined processes decrease overhead expenses.
- Increased Revenue: Faster patient processing boosts service capacity.
Indirect Benefits
- Improved Reputation: Higher patient satisfaction attracts more patients.
- Staff Retention: Smoother workflows reduce burnout.
Estimating Costs
- Training costs for team members.
- Software and tools needed for data collection and analysis.
Leveraging Technology in Lean Six Sigma Projects
Digital Tools for Data Collection
- Electronic Health Records (EHRs): Automatically track patient flow and delays.
- Wearable Sensors: Monitor staff movements to optimize resource allocation.
Automation in Process Improvement
- Automate routine tasks like patient check-in and appointment scheduling.
- Use AI-driven analytics to identify patterns in patient flow data.
Training and Development for Lean Six Sigma in Urgent Care
Customized Training Programs
- Role-Specific Training
- Green Belts: Focus on executing DMAIC phases and validating critical variables (Xs).
- Black Belts: Emphasis on leadership, advanced statistical tools, and mentoring teams.
- Staff: Basic Lean principles and process improvement awareness.
- Simulation-Based Learning
- Conduct real-world scenarios, such as handling high patient volumes, to apply Lean Six Sigma concepts in a controlled environment.
Continuous Education
- Offer certifications (Green Belt, Black Belt) to staff for ongoing professional development.
- Host workshops or online courses to reinforce Lean Six Sigma methodologies.
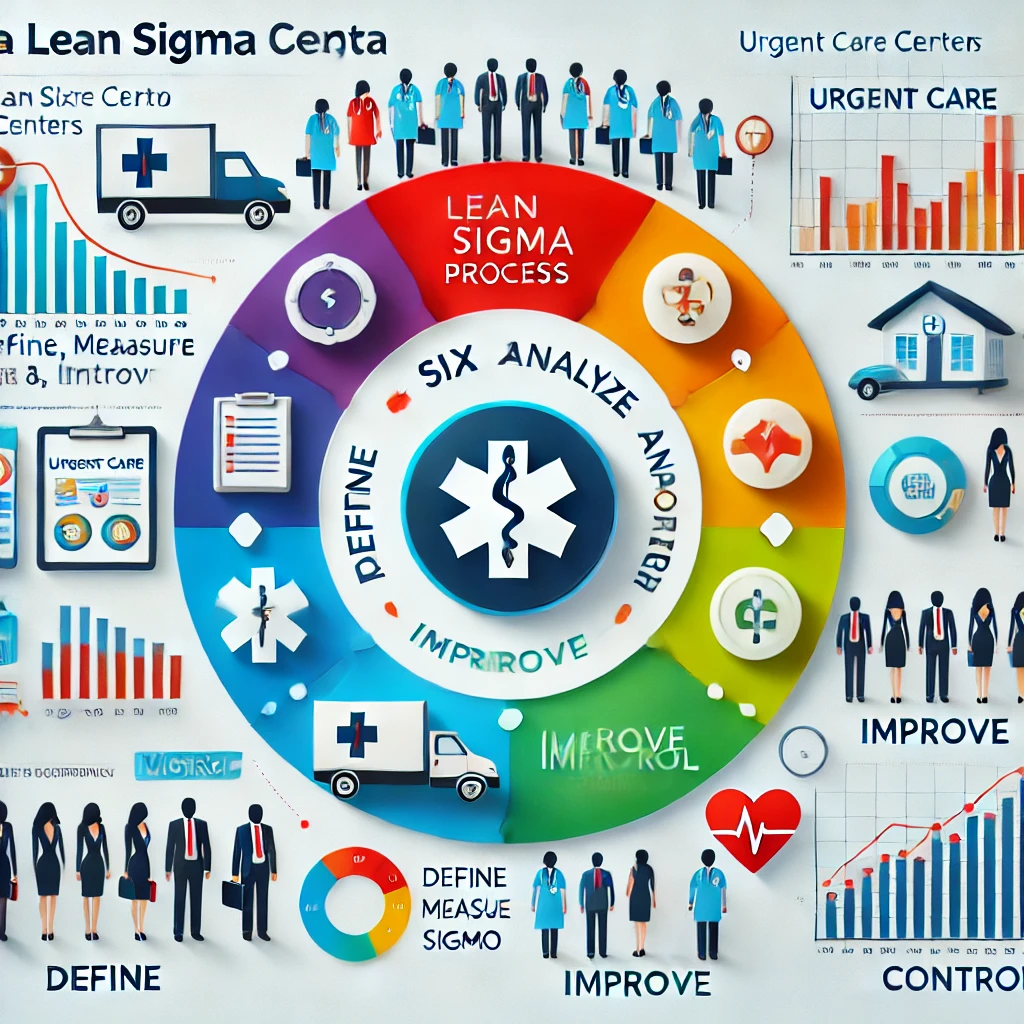
Lean Six Sigma Integration with Healthcare Regulations
Compliance and Quality Standards
- HIPAA: Ensure that process improvements involving patient data adhere to privacy laws.
- The Joint Commission Standards: Align process changes with patient safety and care standards.
Documentation
- Maintain thorough records of Lean Six Sigma projects to demonstrate compliance during audits.
- Use control charts and dashboards to monitor adherence to regulatory requirements.
Using Lean Six Sigma to Improve Patient Flow
Identifying Bottlenecks
- Common bottlenecks include slow triage, delayed lab results, or room availability.
- Use tools like time-motion studies to pinpoint inefficiencies.
Strategies for Improvement
- Triage Optimization: Standardize triage questions and use technology to prioritize cases.
- Room Utilization: Implement real-time tracking of room availability to streamline patient assignments.
- Lab Processing: Introduce automated lab equipment to reduce testing turnaround time.
Expanding Lean Six Sigma Beyond Operations
Enhancing Patient Communication
- Use process mapping to identify and eliminate delays in patient updates.
- Implement automated notification systems for test results and appointment reminders.
Financial Management
- Apply Lean principles to billing cycles to reduce errors and expedite claims processing.
- Validate variables affecting revenue leakage, such as coding inaccuracies or denied claims.
Measuring the Long-Term Impact of Lean Six Sigma
Key Metrics to Track
- Reduction in Wait Times: Sustained decrease in patient wait durations.
- Patient Satisfaction Scores: Monitor long-term trends through periodic surveys.
- Employee Engagement: Measure staff satisfaction and turnover rates post-implementation.
- Cost Savings: Calculate annual savings from reduced waste and improved efficiency.
Establishing Review Cycles
- Conduct quarterly reviews to assess the effectiveness of implemented changes.
- Use dashboards to visualize progress and identify new opportunities for improvement.
Streamlining Scheduling Systems with Lean Six Sigma
Identifying Challenges in Scheduling
- Overlapping Appointments: Double-booking or last-minute changes disrupting schedules.
- Uneven Staff Allocation: Insufficient staff during peak hours, leading to bottlenecks.
- Inefficient Time Slots: Lack of optimized scheduling for common urgent care procedures.
Implementing Solutions
- Demand Forecasting: Use historical data to predict patient volume and align staffing needs.
- Flexible Scheduling Tools: Introduce systems allowing real-time changes based on patient flow.
- Patient Self-Scheduling: Leverage online platforms for patients to book appointments with automated reminders.
Engaging Stakeholders in Lean Six Sigma Projects
Key Stakeholders
- Leadership Team: Ensure alignment with organizational goals and secure necessary resources.
- Frontline Staff: Provide insights into day-to-day operations and identify pain points.
- Patients: Offer feedback on service quality and areas for improvement.
Engagement Strategies
- Regular Updates: Use town halls or newsletters to share project progress.
- Workshops: Train stakeholders on Lean Six Sigma principles relevant to their roles.
- Feedback Loops: Incorporate input from all levels of the organization into project decisions.
Lean Six Sigma for Emergency Preparedness
Preparing for High Patient Volumes
- Develop contingency plans using Lean principles to handle surges in patient numbers, such as during flu season or pandemics.
- Establish clear protocols for triage and resource allocation during emergencies.
Real-Time Monitoring
- Use IoT devices to track critical supplies like PPE and medications.
- Implement dashboards displaying patient flow and staff availability during crises.
Leveraging Lean Six Sigma for Staff Retention
Addressing Staff Burnout
- Root Causes: Analyze factors contributing to burnout, such as extended hours or lack of resources.
- Process Changes: Introduce tools like automated workflows to reduce manual workload and improve job satisfaction.
Recognizing Contributions
- Celebrate milestones achieved through Lean Six Sigma projects, such as reductions in patient wait times.
- Create incentives for participation in process improvement initiatives.
Expanding Lean Six Sigma to Ancillary Services
Lab Services
- Reduce test processing times by streamlining sample handling protocols and adopting advanced lab equipment.
- Use validated Xs to identify variables affecting turnaround time, such as staffing levels or equipment downtime.
Radiology
- Implement Lean principles to minimize wait times for imaging services by optimizing machine usage schedules.
- Train staff on quick yet accurate documentation processes to reduce delays.
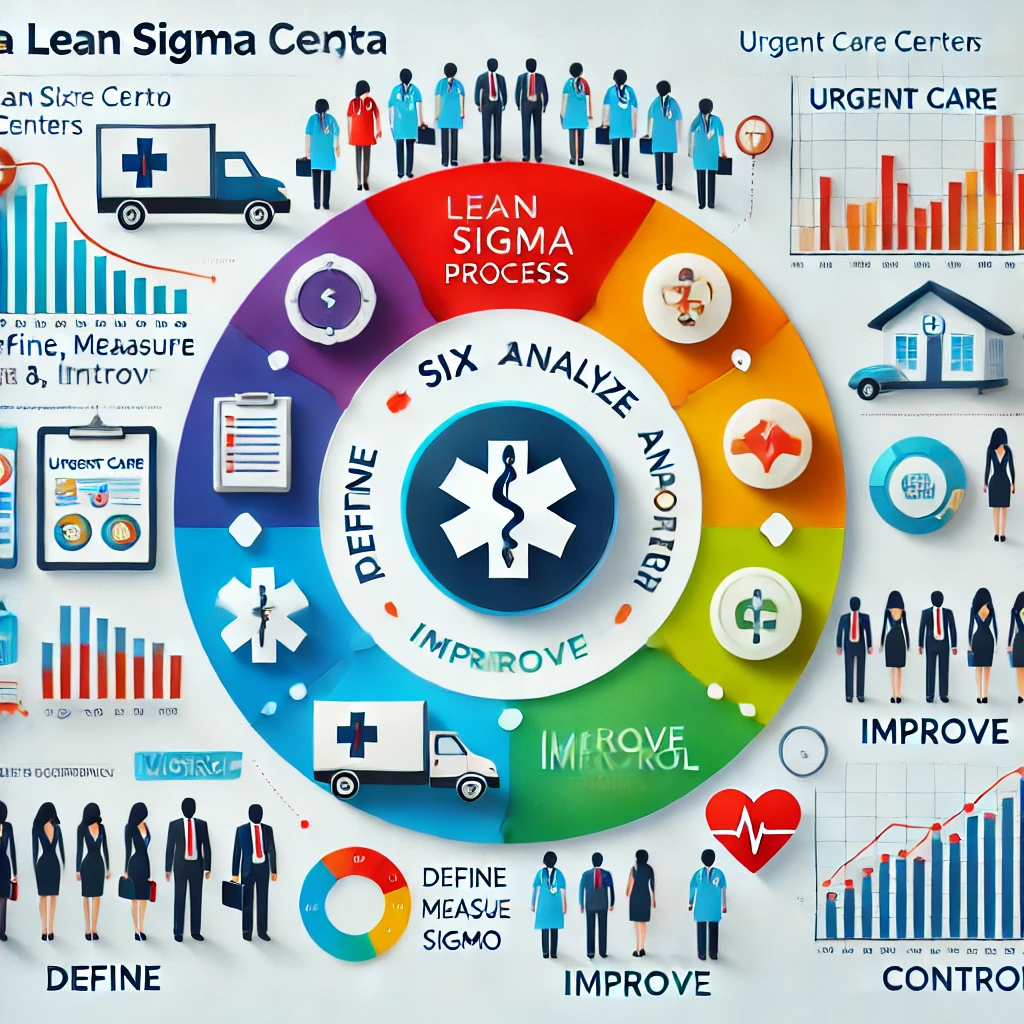
Addressing Common Misconceptions About Lean Six Sigma in Healthcare
Misconception 1: It\u2019s Only for Manufacturing
- Lean Six Sigma is equally effective in healthcare, as it focuses on reducing waste and improving efficiency in any process.
Misconception 2: It\u2019s Too Complex for Small Centers
- Tailored approaches can simplify Lean Six Sigma projects for smaller urgent care centers without overloading resources.
Misconception 3: Results Are Immediate
- While some improvements are quick, sustainable results often require continuous monitoring and refinement.
Creating a Culture of Continuous Improvement in Urgent Care Centers
Building Awareness
- Educational Sessions: Host workshops to introduce Lean Six Sigma principles to all staff members.
- Visual Aids: Display process improvement boards in common areas to highlight ongoing efforts.
Incentivizing Participation
- Recognition Programs: Acknowledge staff contributions to Lean Six Sigma projects.
- Monetary Rewards: Offer bonuses or raises for achieving measurable improvements.
Sustaining Momentum
- Regularly schedule brainstorming sessions for new improvement ideas.
- Celebrate project successes to motivate ongoing efforts.
Optimizing Patient Education Processes with Lean Six Sigma
Challenges in Patient Education
- Misunderstandings about post-care instructions.
- Lack of time for providers to educate patients during busy hours.
Process Improvements
- Standardized Educational Materials: Use printed or digital guides tailored to common conditions.
- Multilingual Resources: Ensure accessibility for patients with diverse language needs.
- Automated Follow-Ups: Implement text or email reminders summarizing key care instructions.
Incorporating Telemedicine into Lean Six Sigma Projects
Benefits of Telemedicine
- Reduces patient wait times for non-critical consultations.
- Optimizes in-person resources for higher acuity cases.
Process Enhancements
- Triage Integration: Use telemedicine as the first step in the patient flow to screen and prioritize cases.
- Scheduling Systems: Ensure seamless scheduling of telemedicine appointments alongside in-person visits.
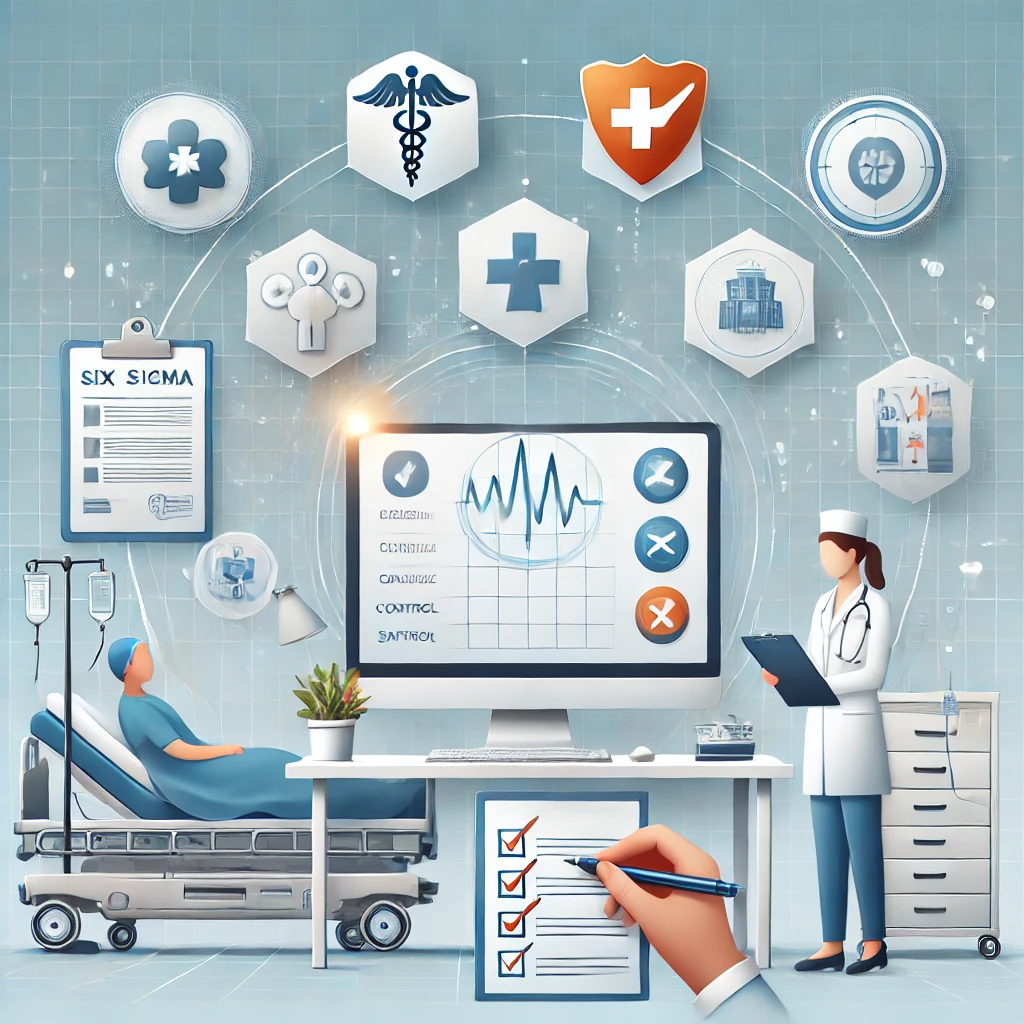
Using Lean Six Sigma to Enhance Patient Safety
Identifying Risks
- Use Failure Mode and Effects Analysis (FMEA) to pinpoint high-risk areas, such as medication administration errors or misdiagnoses.
Safety Interventions
- Barcode Scanning for Medications: Minimize prescription errors.
- Checklists for Procedures: Standardize steps in patient care processes.
- Regular Safety Audits: Monitor compliance with safety protocols and address gaps proactively.
Leveraging Data Analytics for Lean Six Sigma Success
Types of Data to Analyze
- Operational Data: Patient throughput, wait times, and resource usage.
- Outcome Data: Rates of readmissions, complications, or unresolved issues.
- Feedback Data: Patient satisfaction surveys and staff engagement scores.
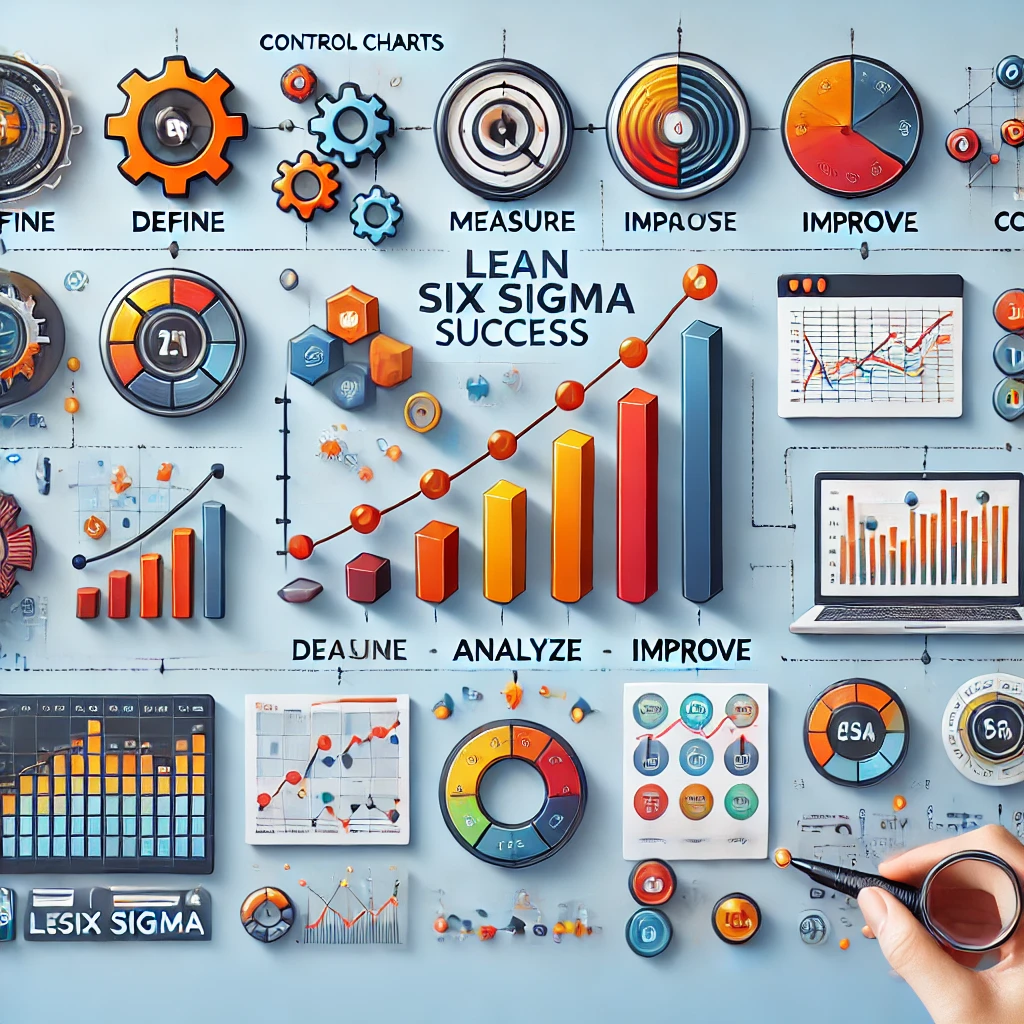
Tools for Analysis
- Dashboards: Visualize trends and anomalies.
- Predictive Analytics: Use historical data to forecast future needs and allocate resources effectively.
Standardizing Triage Processes Using Lean Six Sigma
Current Challenges in Triage
- Inconsistent prioritization of patients based on severity.
- Delays in assigning patients to appropriate care providers.
- Variability in triage times due to staff differences.
Lean Six Sigma Solutions
- Standardized Triage Protocols
- Develop clear, step-by-step guidelines for assessing patient urgency.
- Use decision trees to guide staff through the triage process.
- Technology Integration
- Implement electronic triage tools that automate patient assessment based on input symptoms.
- Use machine learning to predict patient needs and reduce decision-making time.
- Staff Training
- Train all triage staff on the standardized protocols to ensure consistency.
- Conduct role-playing exercises to simulate real-world scenarios.
Addressing Patient Overcrowding with Lean Six Sigma
Causes of Overcrowding
- High patient volumes during peak hours.
- Insufficient staffing and resource allocation.
- Delays in room turnover and discharge processes.
Process Improvements
- Peak Time Analysis
- Use historical data to identify peak hours and days.
- Schedule additional staff and open extra rooms during these times.
- Streamlining Discharges
- Implement electronic discharge summaries to reduce documentation delays.
- Introduce a discharge coordinator role to expedite the process.
- Room Turnover Optimization
- Use time studies to identify and address delays in room cleaning and preparation.
- Develop standardized cleaning protocols to minimize downtime.
Improving Staff Communication and Coordination
Common Issues
- Miscommunication between departments leading to delays.
- Lack of centralized systems for real-time updates.
Enhancements
- Centralized Communication Tools
- Introduce platforms like Slack or Microsoft Teams for instant updates.
- Use shared dashboards to track patient flow and room availability.
- Daily Huddles
- Conduct short, focused team meetings at the start of each shift.
- Use these huddles to review patient priorities and staff assignments.
- Cross-Training Staff
- Train staff across different roles to ensure flexibility during peak hours.
- Enable quick role-shifting to address unexpected surges in patient volume.
Sustaining Lean Six Sigma Improvements
Establishing Continuous Monitoring
- Use KPIs like average patient wait times, satisfaction scores, and throughput rates to track performance.
- Create visual dashboards accessible to staff and leadership for transparency.
Regular Audits
- Schedule monthly reviews of processes to identify new bottlenecks.
- Conduct quarterly workshops to brainstorm and implement further enhancements.
Feedback Loops
- Collect ongoing feedback from patients and staff to identify areas for improvement.
- Use surveys and interviews as part of your review process.
Best Courses and Programs for Lean Six Sigma
1. Purdue University Lean Six Sigma Program
- Comprehensive curriculum covering all levels: White, Yellow, Green, and Black Belt certifications.
- Renowned for integrating theory with practical case studies, including healthcare-focused projects.
- Flexible online and in-person options available.
2. ASQ (American Society for Quality) Certifications
- Globally recognized Lean Six Sigma certifications.
- Offers industry-specific training, including healthcare applications.
- Provides extensive resources, including study guides and practice exams.
3. GoLeanSixSigma.com
- Accessible online training with Green Belt and Black Belt certifications.
- Includes interactive exercises, case studies, and customizable templates.
- Excellent resources tailored for healthcare professionals.
4. Coursera Lean Six Sigma Specializations
- Features courses from universities like Rutgers and the University of Illinois.
- Covers Lean Six Sigma basics to advanced techniques like DOE (Design of Experiments).
- Includes hands-on projects, ideal for urgent care professionals.
5. iCert Global Lean Six Sigma Certification
- Offers fast-track certification programs for working professionals.
- Focuses on real-world applications, including healthcare process improvements.
- Affordable pricing with lifetime access to materials.
Recommended Software for Lean Six Sigma in Healthcare
1. Minitab
- Widely regarded for statistical analysis and process improvement.
- Essential for tasks like regression analysis, control charts, and hypothesis testing.
- User-friendly interface ideal for both beginners and experts.
2. Lucidchart
- Excellent for process mapping and flowchart creation.
- Intuitive drag-and-drop interface, suitable for visualizing patient flow and bottlenecks.
3. Tableau
- Advanced data visualization tool for tracking Lean Six Sigma metrics.
- Useful for creating dashboards to monitor patient wait times, throughput, and satisfaction scores.
4. SigmaXL
- Excel-based software designed for Lean Six Sigma practitioners.
- Includes tools for statistical analysis, DOE, and process mapping.
- Affordable and integrates seamlessly with Microsoft Office.
5. Smartsheet
- Combines project management and Lean Six Sigma tools.
- Helps track DMAIC phases, assign tasks, and collaborate across teams.
- Real-time updates and alerts keep urgent care projects on track.
6. Arena Simulation Software
- Focused on modeling and optimizing complex healthcare processes.
- Ideal for testing scenarios, like managing patient flow during peak hours.
Free and Open-Source Options
1. Google Sheets
- Free and collaborative platform for basic data analysis and tracking.
- Use templates for SIPOC diagrams, Gantt charts, and more.
2. R Programming
- Open-source software for advanced statistical analysis and data visualization.
- Requires programming knowledge but is powerful for complex Lean Six Sigma tasks.
3. Process Street
- Free platform for creating and managing checklists.
- Ideal for documenting and standardizing workflows in healthcare.
Top Platforms for Ongoing Learning
1. Alison
- Offers free courses like “Basics of Lean Six Sigma: Green Belt” and “Learning Lean Six Sigma: Yellow Belt.”
- Covers foundational concepts, with practical healthcare case studies.
2. Udemy
- Affordable courses on topics ranging from Lean Six Sigma fundamentals to advanced statistical tools.
- Includes lifetime access and certifications upon completion.
3. Skillshare
- Features short, engaging courses on Lean Six Sigma principles.
- Great for quick learning modules on specific topics, like waste reduction and process optimization.
4. Process Excellence Network (PEX)
- A hub for Lean Six Sigma professionals, offering webinars, articles, and training programs.
- Focused on best practices and innovations in process improvement.
Best Courses and Programs for Lean Six Sigma
1. Purdue University Lean Six Sigma Program
- Comprehensive curriculum covering all levels: White, Yellow, Green, and Black Belt certifications.
- Renowned for integrating theory with practical case studies, including healthcare-focused projects.
- Flexible online and in-person options available.
2. ASQ (American Society for Quality) Certifications
- Globally recognized Lean Six Sigma certifications.
- Offers industry-specific training, including healthcare applications.
- Provides extensive resources, including study guides and practice exams.
3. GoLeanSixSigma.com
- Accessible online training with Green Belt and Black Belt certifications.
- Includes interactive exercises, case studies, and customizable templates.
- Excellent resources tailored for healthcare professionals.
4. Coursera Lean Six Sigma Specializations
- Features courses from universities like Rutgers and the University of Illinois.
- Covers Lean Six Sigma basics to advanced techniques like DOE (Design of Experiments).
- Includes hands-on projects, ideal for urgent care professionals.
5. iCert Global Lean Six Sigma Certification
- Offers fast-track certification programs for working professionals.
- Focuses on real-world applications, including healthcare process improvements.
- Affordable pricing with lifetime access to materials.
Recommended Software for Lean Six Sigma in Healthcare
1. Minitab
- Widely regarded for statistical analysis and process improvement.
- Essential for tasks like regression analysis, control charts, and hypothesis testing.
- User-friendly interface ideal for both beginners and experts.
2. Lucidchart
- Excellent for process mapping and flowchart creation.
- Intuitive drag-and-drop interface, suitable for visualizing patient flow and bottlenecks.
3. Tableau
- Advanced data visualization tool for tracking Lean Six Sigma metrics.
- Useful for creating dashboards to monitor patient wait times, throughput, and satisfaction scores.
4. SigmaXL
- Excel-based software designed for Lean Six Sigma practitioners.
- Includes tools for statistical analysis, DOE, and process mapping.
- Affordable and integrates seamlessly with Microsoft Office.
5. Smartsheet
- Combines project management and Lean Six Sigma tools.
- Helps track DMAIC phases, assign tasks, and collaborate across teams.
- Real-time updates and alerts keep urgent care projects on track.
6. Arena Simulation Software
- Focused on modeling and optimizing complex healthcare processes.
- Ideal for testing scenarios, like managing patient flow during peak hours.
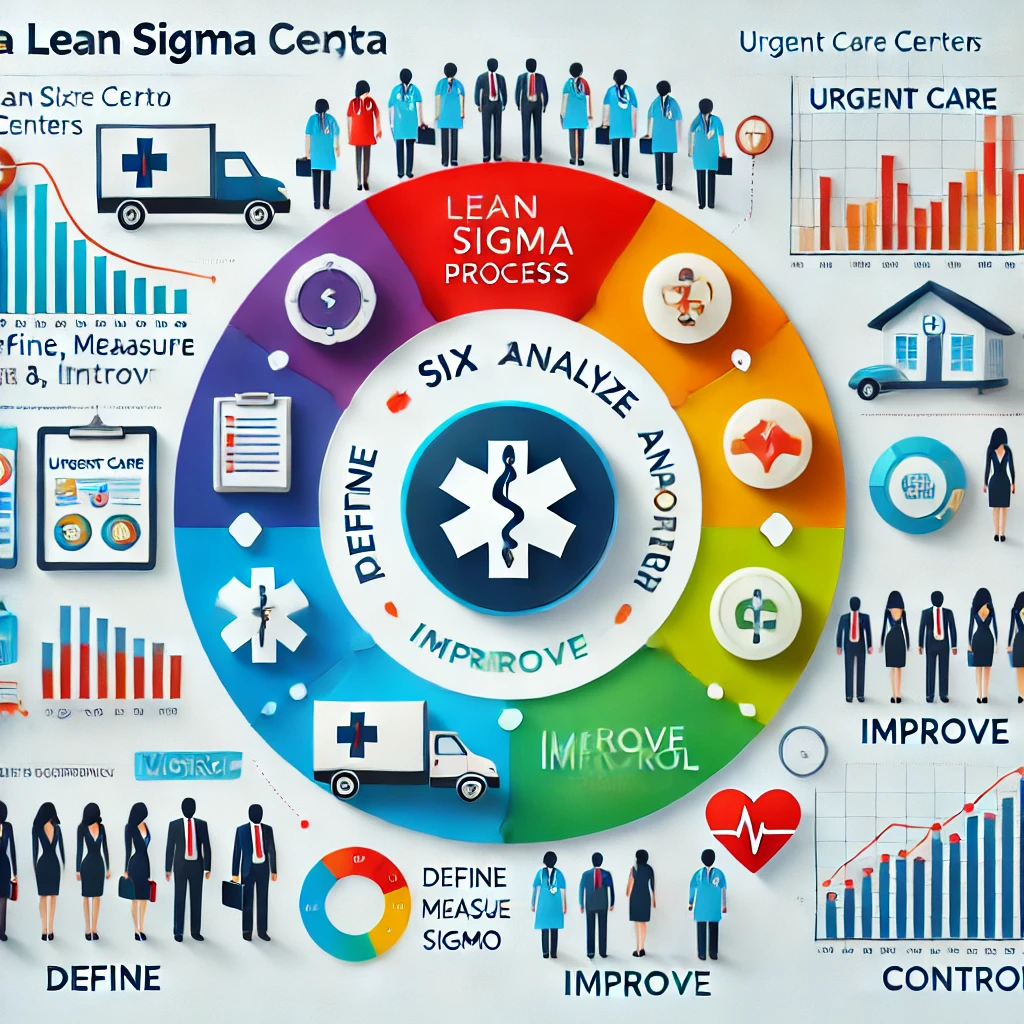
Free and Open-Source Options
1. Google Sheets
- Free and collaborative platform for basic data analysis and tracking.
- Use templates for SIPOC diagrams, Gantt charts, and more.
2. R Programming
- Open-source software for advanced statistical analysis and data visualization.
- Requires programming knowledge but is powerful for complex Lean Six Sigma tasks.
3. Process Street
- Free platform for creating and managing checklists.
- Ideal for documenting and standardizing workflows in healthcare.
Top Platforms for Ongoing Learning
1. Alison
- Offers free courses like “Basics of Lean Six Sigma: Green Belt” and “Learning Lean Six Sigma: Yellow Belt.”
- Covers foundational concepts, with practical healthcare case studies.
2. Udemy
- Affordable courses on topics ranging from Lean Six Sigma fundamentals to advanced statistical tools.
- Includes lifetime access and certifications upon completion.
3. Skillshare
- Features short, engaging courses on Lean Six Sigma principles.
- Great for quick learning modules on specific topics, like waste reduction and process optimization.
4. Process Excellence Network (PEX)
- A hub for Lean Six Sigma professionals, offering webinars, articles, and training programs.
- Focused on best practices and innovations in process improvement.
Would you like detailed recommendations for any specific aspect, such as Green Belt certifications or software comparisons?
You said:
yes please both
ChatGPT said:
ChatGPT
Detailed Recommendations for Green Belt Certifications
1. Purdue University Lean Six Sigma Green Belt
- Overview: A comprehensive program that combines online modules with practical case studies.
- Highlights:
- Focus on the DMAIC methodology.
- Real-world applications, including healthcare-focused projects.
- Support from experienced instructors.
- Cost: Mid-range pricing with payment plan options.
- Best For: Professionals looking for an academic-backed certification.
2. ASQ Certified Six Sigma Green Belt (CSSGB)
- Overview: Globally recognized certification focusing on process improvement and statistical methods.
- Highlights:
- Covers a wide range of industries, including healthcare.
- Rigorous exam with preparatory materials provided.
- Access to ASQ’s extensive network of quality professionals.
- Cost: Exam fee is approximately $438 (non-member), with discounts for ASQ members.
- Best For: Individuals seeking a respected, globally recognized credential.
3. GoLeanSixSigma.com Green Belt
- Overview: Online training with a focus on practical implementation.
- Highlights:
- Interactive modules and simulations.
- Step-by-step DMAIC framework for project execution.
- Flexible self-paced format.
- Cost: Affordable pricing with group discounts available.
- Best For: Busy professionals or teams needing flexibility.
4. Coursera Lean Six Sigma Green Belt Specialization
- Overview: A university-backed certification program.
- Highlights:
- Hosted by the University of Illinois or Rutgers University.
- Combines theoretical knowledge with practical projects.
- Flexible scheduling and subscription-based cost structure.
- Cost: Approximately $50/month (varies by duration).
- Best For: Learners who value academic affiliation and hands-on projects.
Software Comparisons for Lean Six Sigma
1. Minitab
- Features:
- Statistical analysis tools like control charts, regression, and hypothesis testing.
- Easy-to-use interface with robust visualizations.
- Tailored templates for Lean Six Sigma projects.
- Pros:
- Industry standard for Six Sigma professionals.
- Extensive documentation and support.
- Highly reliable for advanced analytics.
- Cons:
- Expensive for small organizations.
- Best For: Professionals needing precise statistical analysis.
2. SigmaXL
- Features:
- Excel add-on for statistical and graphical analysis.
- Includes process capability, DOE, and Monte Carlo simulations.
- Pros:
- Affordable and easy to integrate with existing Excel workflows.
- Ideal for beginners and intermediate users.
- Cons:
- Limited capabilities compared to standalone software like Minitab.
- Best For: Budget-conscious teams with basic statistical needs.
3. Lucidchart
- Features:
- Tools for process mapping, flowcharting, and SIPOC diagrams.
- Collaborative real-time editing for team projects.
- Pros:
- Highly intuitive and visually appealing.
- Cloud-based with easy sharing capabilities.
- Cons:
- Limited statistical analysis tools.
- Best For: Teams focused on process visualization.
4. Tableau
- Features:
- Advanced data visualization with dashboards.
- Integration with various data sources for real-time insights.
- Pros:
- Excellent for presenting Lean Six Sigma results to stakeholders.
- Interactive dashboards for ongoing monitoring.
- Cons:
- Requires a learning curve for advanced features.
- Best For: Teams focused on data interpretation and communication.
5. Arena Simulation Software
- Features:
- Simulates process flows to test potential improvements.
- Ideal for modeling complex healthcare systems like patient flow.
- Pros:
- Helps visualize and analyze proposed changes before implementation.
- Great for predictive modeling.
- Cons:
- Expensive and requires specialized training.
- Best For: Healthcare centers with complex systems requiring detailed modeling.
6. Google Sheets with Add-ons
- Features:
- Free platform for tracking and analyzing data.
- Add-ons like QI Macros enhance Lean Six Sigma capabilities.
- Pros:
- Cost-effective and collaborative.
- Accessible for teams of all sizes.
- Cons:
- Limited scalability for large datasets.
- Best For: Small teams and organizations just starting with Lean Six Sigma.
Final Thoughts
Embarking on a Lean Six Sigma project in an urgent care center represents a commitment to excellence in patient care and operational efficiency. This methodology provides the tools to identify inefficiencies, implement meaningful improvements, and create a sustainable culture of continuous enhancement.
As healthcare continues to evolve, the principles of Lean Six Sigma remain timeless. By reducing waste, streamlining processes, and focusing on validated variables (Xs), urgent care centers can not only meet but exceed patient expectations. From minimizing wait times to optimizing staff allocation, the potential for transformation is immense.
Lean Six Sigma is not just about fixing problems; it’s about proactively designing systems that anticipate and prevent issues before they arise. This proactive approach fosters trust among patients, empowers staff, and positions urgent care centers as leaders in quality and innovation.
Remember, the success of any Lean Six Sigma initiative depends on teamwork, clear communication, and a shared vision for improvement. By engaging all stakeholders, leveraging the right tools, and maintaining a patient-centric focus, your urgent care center can achieve measurable and lasting success.
Let this guide serve as a starting point for your journey toward operational excellence. The path may be challenging, but the rewards—improved efficiency, better patient outcomes, and higher satisfaction—make every effort worthwhile.